What is Pharma 4.0?
Pharma 4.0, which originated in 2017 through ISPE, is a comprehensive manufacturing approach derived from Industry 4.0. It encompasses the Industry 4.0 operating model, focusing on its application to the production of medicinal products. Pharma 4.0 streamlines and optimizes manufacturing processes through digitalization, which leads to increased efficiency, reduced production time, and minimized waste, ultimately enhancing overall productivity.
Digitalization
At present, in most organizations, frequent analytical characterization and quality testing of the intermediate drug substance and final drug product at various points of the manufacturing process are unorganized, scattered in different computer locations, and handled by different teams. This lack of cohesion and integration hinders efficiency, data accessibility, and decision-making capabilities within the pharmaceutical industry.
To address these challenges and embrace the transformative potential of Pharma 4.0, organizations need to take proactive steps. As a pharmaceutical organization, your first step towards Pharma 4.0 would be assessing your digital maturity. By evaluating your organization in six different areas—computerization, connectivity, visibility, transparency, productivity, and adaptability—you can identify areas for improvement and chart a path toward digital transformation. Remember that your digitalization won’t happen overnight, however, by taking simple yet meaningful steps, you can gradually move closer to Pharma 4.0.
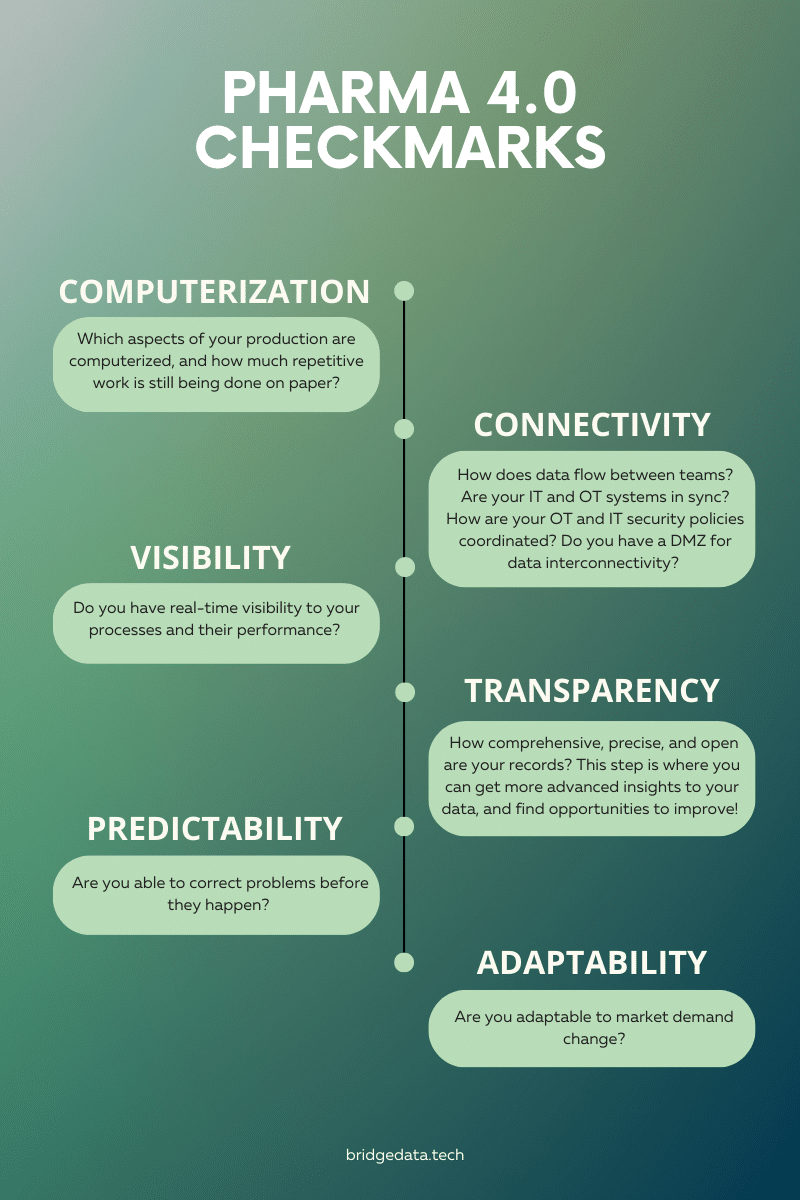
- Computerization: Which aspects of your production are computerized, and how much repetitive work is still being done on paper?
- Connectivity: How does data flow between teams? Are your IT and OT systems in sync? How are your OT and IT security policies coordinated? Do you have a DMZ for data interconnectivity?
- Visibility: Do you have real-time visibility of your processes and their performance?
- Transparency: How comprehensive, precise, and open are your records? This step is where you can get more advanced insights into your data and find opportunities to improve!
- Predictability: Are you able to correct problems before they happen?
- Adaptability: Are you adaptable to market demand change?
Quality Control
Continuous monitoring and real-time handling of deviations
ML-powered techniques can analyze existing data in pharmaceutical manufacturing facilities to monitor the impact of material property discrepancies, procedure variations, and process anomalies like sensor drift and environmental conditions fluctuations that may affect the final product. Continuous monitoring is particularly beneficial in sterilization processes, such as steam sterilization or autoclaving, which are essential for ensuring product sterility. Monitoring variables like temperature, pressure, and exposure time ensures effective sterilization and compliance with regulatory requirements.
While condition monitoring isn’t new for operations like sterilization, historical data including process parameters in batch operations can help establish a baseline for normal operating conditions, and by comparing this baseline of critical process parameters during operation, deviations can be detected. This approach enables more accurate and earlier detection of anomalies compared to the traditional method of setting alarms based on system variable limits. Other processes that could also benefit from continuous monitoring and detecting a deviation in their batch operations include Cleaning in Place (CIP) cycles, Tangential Flow Filtration (TFF), and chromatography operations.
Filling and Packaging
Continuous monitoring of variables in the filling and packaging process, such as fill weight, seal integrity, and labeling accuracy, can help ensure accurate dosing, proper sealing, and correct labeling of pharmaceutical products.
Package and Seal integrity are critical in this industry, and many manufacturers use human operators to verify package integrity and sterility, which is labor-intensive and can be inconsistent at times. A deep-learning vision-based system can capture high-resolution images of the sealed packages and products, and analyze them for any irregularities, such as gaps, wrinkles, or improper alignment. By comparing the captured images to reference images of properly sealed packages, the vision system can identify potential seal defects.
Labeling accuracy: A vision system can scan labels on packaged pharmaceutical products and verify their accuracy and placement. It can read the text, verify barcodes or QR codes, and check for alignment and legibility. By comparing the scanned information with the expected labeling specifications, the vision system can identify any errors or discrepancies. This helps prevent mislabeling, incorrect dosage instructions, or product mix-ups.
Predictive Maintenance in Pharmaceutical Manufacturing
Over 80% of equipment failures in manufacturing are caused by poor operating conditions or human error, rather than wear and tear over time. The pharmaceutical industry heavily depends on the quality and accuracy of the manufacturing equipment. The failure of vital equipment such as bioreactors, which are essential to produce biopharmaceuticals, vaccines, and other biological products, could result in a loss of over $30,000 per batch. AI-powered predictive maintenance monitors your equipment at all times and helps prevent costly unplanned downtime and lost production. The AI algorithm learns the normal operating patterns of equipment by collecting data on variables such as temperature, pressure, and agitation speed, and will predict failures before they occur.
Examples of other equipment that could hugely benefit from this technology include tablet compression machines and chromatography systems.
The future of biopharma lies in the integration of Industry 4.0 technologies such as AI and ML. Bridge Automation stands at the forefront of this transformative era, capable of revolutionizing pharmaceutical development, manufacturing, and delivery. Join us on this journey as we unlock new possibilities, drive innovation, and shape the future of healthcare together.
To learn more about our solutions, schedule a consultation.